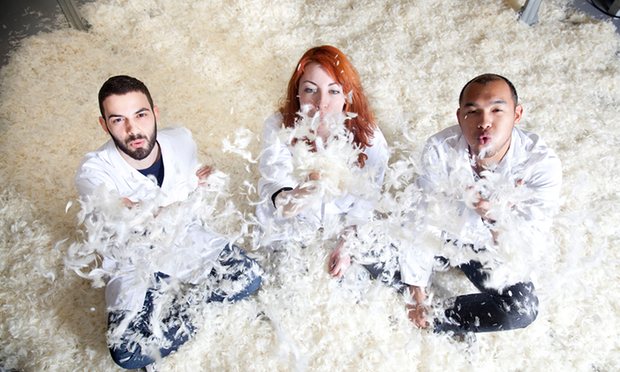
The innovators: greener home insulation to feather your nest
The ability of chickens to stay warm in winter has inspired a new energy-efficient home insulation product developed by students at Imperial College London.
Around 900m chickens are slaughtered each year by the poultry industry, producing 2,000 tonnes of feather waste a week, most of which ends up in landfill or goes through an energy-intensive process to be made into animal feed. But what else could be done with it?
As part of her research into potential uses for feather waste, design engineering student Elena Dieckmann ordered a 10kg box of excess feathers from about 70 chickens. At first, she had no idea what they might be used for, but soon the answer became obvious: in the same way that feathers protect chickens from the cold, they can keep people’s homes warm.
Dieckmann and two fellow students – chemical engineer Ioannis Tzouganatos and biologist Ryan Robinson – are now developing a method to mix chicken feathers with the foam used in home insulation boards. They want to create a potentially cheaper – and greener – home insulation alternative.
The students teamed up after being tasked with finding a suitable use for the feathers by Imperial College’s Professor Chris Cheeseman.
“Feathers are made for protecting chickens or birds from water and cold. This is what we are targeting to replicate in our product, FeatherFill – to use these properties to create better insulating material,” says Tzouganatos.
“We thought about what feathers are good for – there is obviously a lot of inspiration from nature,” says Robinson.
“It was a very experimental approach,” adds Dieckmann. “Can we use the amazing properties of feathers in another material? It’s obvious now that insulation would make sense, because [the feathers were] air-trapping.”
The result of their research is a way to replace some of the polyurethane foam contained in boards commonly used in home insulation. Substituting blended feathers for about 30% of the foam produces a cheaper material with similar heat-retention qualities. It provides a use for the unwanted feathers, creating a circular economy.
The feathers are blended with the foam to create a material with consistent properties. Feathers that do not end up in landfill are typically used to produce animal feed called feather meal.
The students used probes to measure the thermal conductivity of the new material – how effectively heat passes through it – and found it had similar values to other products on the market. Dieckmann says that by replacing 30% of the synthetic materials in the foam with ground feathers, the same effect could be achieved at a lower cost. The price of the foam was 14 times that of the processed feathers, she says.
Adding more feathers does not automatically result in a more effective product, however. “The thing is, when you are making the foam, it is at first at liquid state and then it rises. But if you put too many solids in it, then it just does not rise, so you don’t end up with a foam – you just end up with something like cement,” says Tzouganatos. “You have to find the optimum window.”
A final product, possibly a foam board, could be ready within months; the students say that the fundamentals of their creation are sound, although they are still working on improvements. Tests will be carried out for mould resistance and flammability.
Because the raw material is cheap, the new product could lower the cost of insulation for homeowners, Robinson says. “The problem is, especially in London, that a lot of our houses are quite old and so they don’t have proper insulation in them. So we are wasting money and energy.”
Ideally all houses should be insulated, but there are a number of barriers to that including cost, awareness and the lack of government incentives. “We are hoping that by reusing a waste product, you can lower the cost instead of having to process all of these extra materials,” says Robinson.
The vast majority of the 2,000 tonnes of poultry feathers produced each week are from chickens, and slaughterhouses pay £63 per tonne to dispose of them, Robinson says. The industry is therefore looking for commercial and environmental alternatives to the current system. “They are already paying to get rid of them, so they might just pay us less,” he says.
The students recently won £20,000 of funding for the idea from the 2016 Mayor of London’s Low Carbon Entrepreneur competition. They also want to examine whether the product could be used as a flexible foam that is pumped into wall cavities.
Among the trials and errors that got the group to FeatherFill was an attempt to make a lightweight cement. The idea that some people might be squeamish about having chicken feathers in their walls or roofs does not concern them, however.
“We don’t know why someone would say that. You wouldn’t see it, you wouldn’t smell it. It is not that we slaughtered the chicken to make the foam. They are already slaughtered and we just utilise the feathers, so we are not really concerned about it,” says Tzouganatos