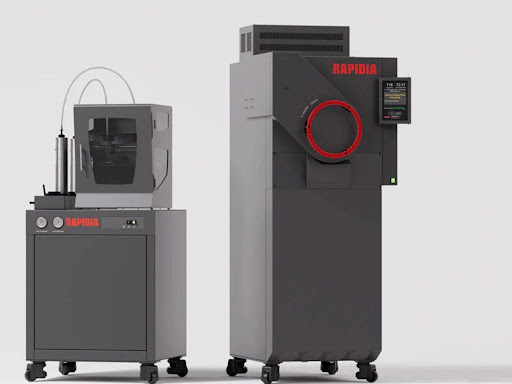
Metal vs. Plastic: Why Metal 3D Printing is Gaining Traction in Prototyping
This shift is primarily due to advancements in technology, increased demand for durable parts, and a growing understanding of the benefits that metal 3D printers bring to the table.
In the realm of additive manufacturing, the battle between metal and plastic 3D printing continues to heat up. While plastic 3D printing has long been the go-to method for prototyping due to its affordability and ease of use, metal 3D printing is rapidly gaining traction as a preferred choice for various industries. This shift is primarily due to advancements in technology, increased demand for durable parts, and a growing understanding of the benefits that metal 3D printers bring to the table.
The Rise of Metal 3D Printing
Traditionally, prototyping with metal was seen as a complicated and expensive endeavor. However, innovations in metal 3D printers have revolutionized this landscape. Modern machines, such as the Creality K1, have made it easier and more cost-effective to produce complex metal components with high precision. These advancements have democratized access to metal 3D printing, allowing smaller companies and startups to leverage this technology without the prohibitive costs that were once associated with it.
Advantages of Metal 3D Printing
- Durability and Strength: Metal parts inherently possess superior mechanical properties compared to their plastic counterparts. For applications requiring high strength, heat resistance, and durability—such as in aerospace, automotive, and medical industries—metal 3D printing is the clear winner. The ability to produce intricate geometries that traditional manufacturing methods can't achieve also plays a significant role in the material's rising popularity.
- Complex Geometries: Metal 3D printers can produce complex designs that would be impossible or economically unfeasible with traditional machining. For example, lattice structures that provide strength without unnecessary weight can be easily printed, leading to more efficient designs. This capability allows engineers and designers to push the boundaries of innovation, creating lightweight yet strong components.
- Material Versatility: With advancements in metal 3D printing technology, various materials can now be used, including titanium, aluminum, and stainless steel. This versatility opens up a world of possibilities for prototyping different parts, depending on the specific requirements of the project. By selecting the appropriate metal, designers can optimize their prototypes for specific conditions and applications.
- Rapid Prototyping: Time-to-market is critical in today’s competitive landscape. Metal 3D printing significantly reduces the time required for prototyping compared to traditional methods. With metal 3D printers like the Creality K1, parts can be designed, printed, and tested in a fraction of the time it would take using traditional machining techniques. This speed enables companies to iterate faster and make data-driven decisions more efficiently.
- Cost-Effectiveness in the Long Run: While the initial investment in metal 3D printing may be higher than plastic 3D printing, the long-term benefits can outweigh these costs. Fewer material waste, reduced labor costs, and the elimination of multiple manufacturing steps contribute to overall savings. Companies often find that investing in metal 3D printers ultimately leads to lower production costs when considering the entire lifecycle of a product.
Plastic 3D Printing: Where It Stands
Plastic 3D printing remains an essential technology, particularly for rapid prototyping and low-cost models. Materials like PLA and ABS are excellent for creating visually appealing prototypes and functional parts without the complexities associated with metal. However, for industries demanding higher performance and durability, plastic often falls short.
Moreover, while plastic parts can be produced quickly, they may not provide the necessary mechanical properties required for functional testing in certain applications. This is where metal 3D printing shines, offering a more robust solution for demanding environments.
Conclusion
As businesses and innovators in Canada look to push the envelope in product development, the availability of advanced 3D printers in Canada is making it easier than ever to embrace this technology. As the demand for metal 3D printing continues to rise, it’s evident that the future of prototyping lies in the powerful capabilities of metal 3D printers.